Magnetic Chip Conveyors: The Essential Resolution for Environment friendly Steel Chip Removing
BusinessMagnetic chip conveyors are an essential part of many industrial processes, especially in environments where large quantities of metal chips are generated. Metalworking operations like machining, grinding, and cutting create significant amounts of metal debris, which need to be removed efficiently to ensure smooth production. The chips can be sharp and fine and may contain lubricants and oils. This makes manual handling difficult and time-consuming. Magnets are used to transport and collect ferrous metal chip materials from the work area to designated recycling bins. This automated solution eliminates the need for manual handling, improving safety, efficiency, and cleanliness in manufacturing environments.
Magnetic chip conveyors are able to transport ferrous metals such as steel, iron and other magnets that are produced by machining. These metals are often challenging to manage because of their sharp edges and tendency to pile up or become tangled in traditional conveyor systems. Magnet conveyors solve this problem by embedding powerful magnets in the belt, or placing them beneath the surface. Magnets produce a magnetic force that holds ferrous material in place as it moves along a conveyor. The magnetic field prevents metal chips falling or being misaligned. This ensures that the chips are transported safely to the designated point. The use of this method to handle metal chips improves efficiency, safety and reduces manual labor.
The versatility of magnetic chip conveyors is also well-known. These systems can be customized to meet the specific needs of different industries and applications. Magnetic conveyors are designed for the specific layout of your production facility, whether it is horizontal, vertical, or inclined. They can also be configured to handle various chip sizes, from small metal filings to larger, bulkier metal shavings. The magnetic field strength can be changed depending on the weight and size of the material being moved. This adaptability allows businesses to optimize their conveyor systems for the specific demands of their production lines, whether they are dealing with heavy-duty scrap metal or fine metal particles. The ability to customize the system ensures that magnetic chip conveyors can be used in a wide range of metalworking environments, from small workshops to large industrial plants.
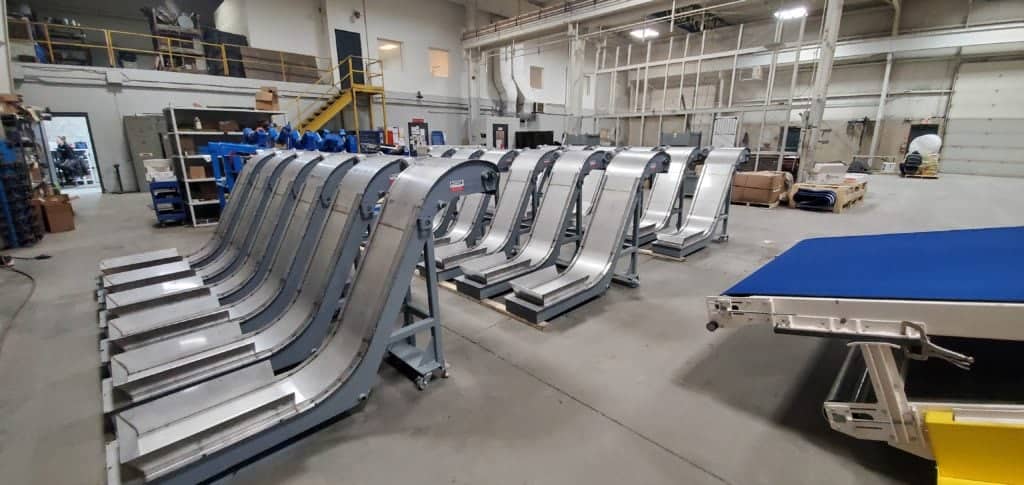
Magnetic chip conveyors can improve operational efficiency while reducing downtime. The traditional Magnetic Chip Conveyors relies on friction in order to move the materials. This can wear out belts, components, and cause increased maintenance and repairs. Magnet conveyors operate without friction, as they use magnets to hold the chips on the belt. The system lasts longer, and maintenance is less expensive because of the reduced friction. Magnetic conveyors also help to streamline the production process by eliminating manual handling of chips and minimising material contamination or loss. Material flow is continuous and efficient, ensuring that the production line remains operational and uninterrupted. To get supplementary details kindly head to Tecnimetal
Magnetic chip conveyors also improve workplace safety and hygiene. The metal chips can be sharp, and if left on the ground or near equipment they could pose a danger to workers. Metal chips, when mixed with oil or lubricants, can create fire hazards in some industries. These risks can be mitigated by magnetic chip conveyors, which collect and move the chips from working areas. This not only ensures a safer work environment but also prevents equipment from becoming clogged with debris. Magnetic chip conveyors reduce the risks of injuries and accidents by keeping the area they work in clean.
Safety is another area where magnetic chip conveyors offer significant benefits. The sharpness of metal chips can be dangerous in environments that are involved with metalworking, such as those that require machining, cutting or grinding. When these chips accumulate on the floor or around equipment, they pose a risk to workers, who could be injured by stepping on or coming into contact with them. Furthermore, in some cases, metal chips mixed with oils or lubricants can create fire hazards. Magnetic chip conveyors allow industries to automate metal chip removal, eliminating the need for handling by hand and minimising the risk associated with metal debris. The work environment is cleaner and safer, as workers are not exposed to dangerous metal pieces. Magnetic chip conveyors improve worker safety by reducing manual work and stopping metal chips from collecting in dangerous areas.